Airbus Defence and Space Bremen
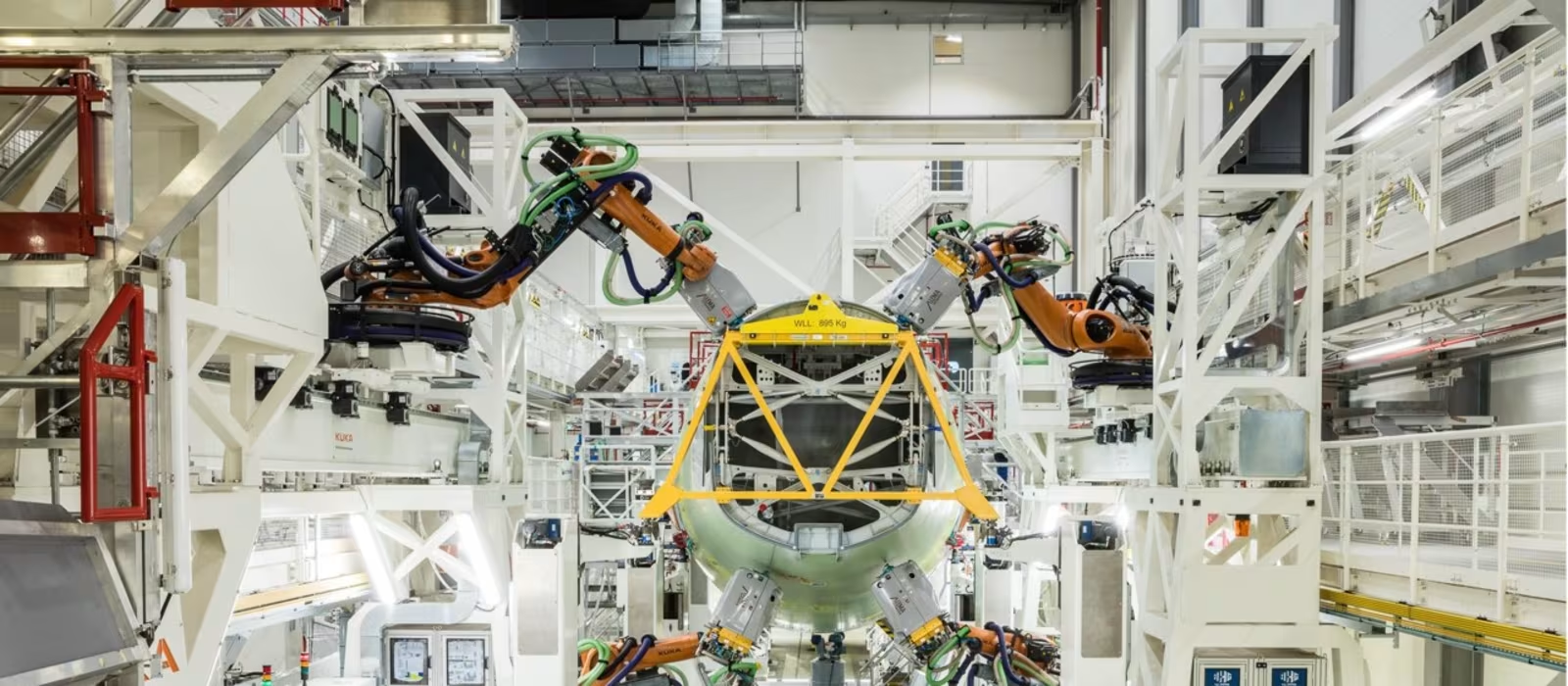
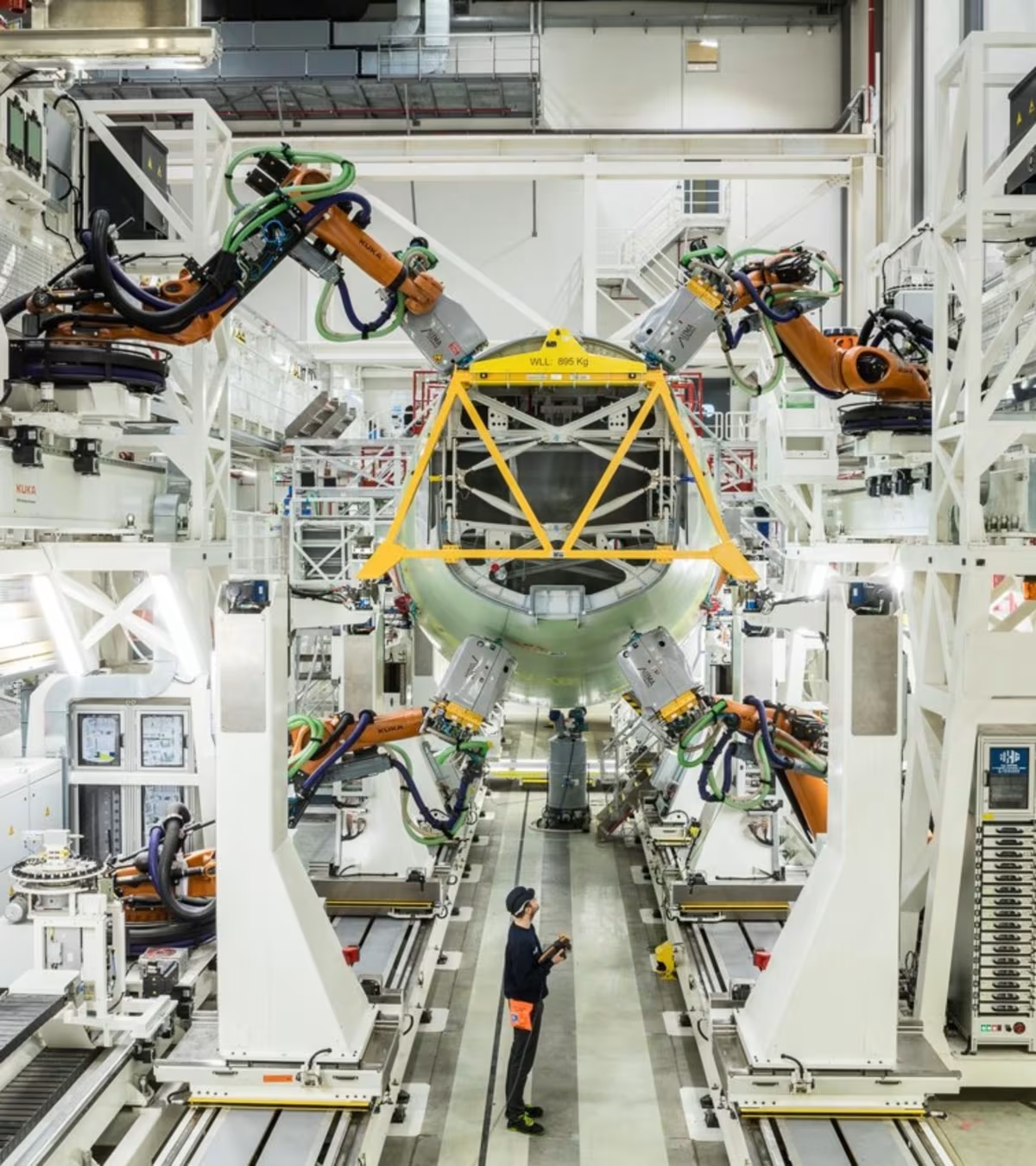
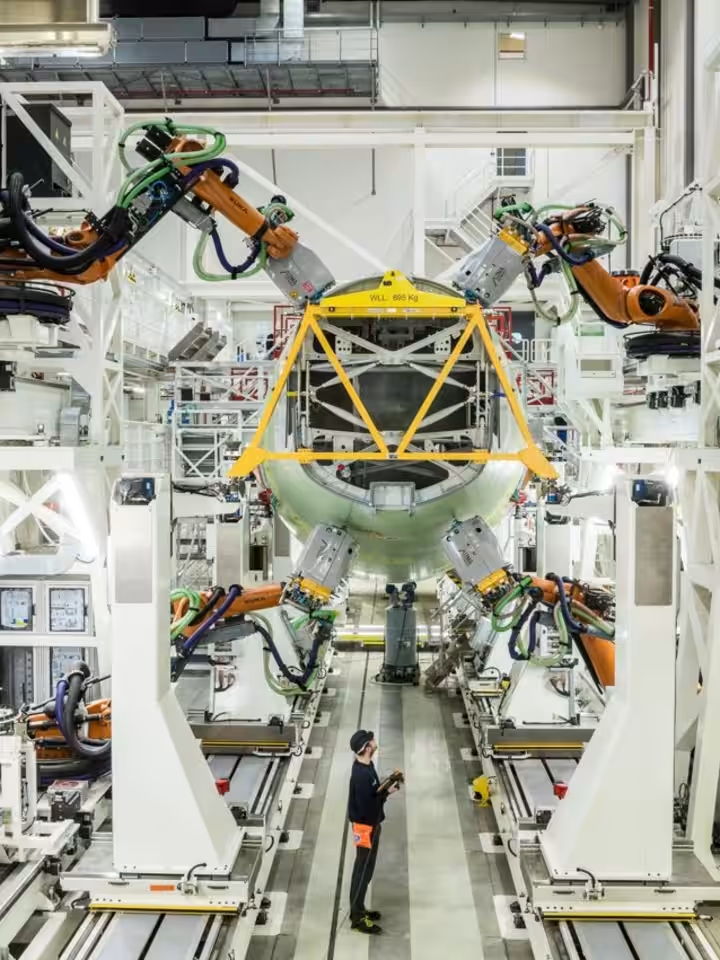
Results of the long-term study eagerly awaited
Ensuring occupational safety and improving the ergonomics of their colleagues is the task of Boris Ruschkowski, Safety Officer, and Christian Boehm, Occupational Safety Specialist at Airbus Defense and Space in Bremen. Together with BG ETEM* and DGUV**, eight employees and SUITX by Ottobock, they have been testing whether exoskeletons are a valuable addition since October 2022. The evaluation of the extensive data material began in February 2024. The results of the study are eagerly awaited, and not only at Airbus.
Franziska Christians is one of the eight Airbus employees taking part in the study. Christians' work in the fuselage of a future aircraft also involves pulling rivets, most of them above shoulder and head height. This puts a strain on the musculoskeletal system. The arms get tired quickly. To take breaks, the activity is interrupted time and again. Productivity suffers and errors can creep in. The shoulder exoskeleton, which is worn close to the body, is designed to relieve Christians' shoulder muscles.
Vanessa Dembski is also taking part in the study. Among other things, she equips the aircraft with hydraulic lines. This also requires her to hold her arms above shoulder height for most of the time. The two young women are testing the IX SHOULDER, one of SUITX's passive exoskeletons. These use the body's own strength and do not require any external energy supply. This makes the exoskeletons light and easy to handle and the muscles are still used, just no longer overloaded.
Long-term study
The study, which has been running since October 2022, is being scientifically monitored by the Institute for Occupational Safety and Health of the DGUV (IFA). One of the questions to be answered is whether the use of an exoskeleton can lead to muscle atrophy. Electro-myography, an examination method that uses sensors to measure muscle activity, is also being used for this purpose. Initial results are promising.
However, Airbus will only decide whether and how the exoskeletons will be used once the study has been completed.
Did you know?
The first exchange between Ottobock and Airbus took place back in 2019. The CX EASY NECK was developed as a result of the constructive collaboration at that time. The Neck complements the IX SHOULDER. It works like a hammock for the head and relieves pressure on the cervical spine.
Read the full article from Frank Siemers (p. 8f.):
„Das Magazin für Sicherheitsbeauftragte Arbeit & Gesundheit“ (BG ETEM, Edition 3/2024, German article)
* BG ETEM: German Employers' Liability Insurance Association for Energy, Textiles, Electrical and Media Products
** DGUV: German Social Accident Insurance
Join the innovation
Are you interested in SUITX products for your industry, customer markets or want to join forces with us? Or would you like to find out more about our new products IX BACK VOLTON and AIRGO XP? Let's get in touch.